Conveyor Sprocket
Conveyor sprockets are the backbone of efficient material handling systems, driving chains to move goods smoothly across industries. TEBSA, based in Argentina since 1997, crafts high-quality conveyor sprockets that power everything from grain silos in the Pampas to food processing plants in Buenos Aires. Our sprockets, built with precision and durability, ensure seamless operation in demanding environments. With a 100% quality guarantee and a 50% cost advantage over original brands, TEBSA delivers reliable solutions backed by a team that responds within 24 hours. Designed to mesh perfectly with conveyor chains, our sprockets transfer motion with minimal friction, reducing wear and boosting productivity. Made from materials like high-grade steel, stainless steel, and aluminum, they withstand corrosion, heavy loads, and harsh conditions. Whether you’re in agriculture, manufacturing, or mining, TEBSA’s conveyor sprockets keep your operations running. From standard designs to custom orders, we tailor solutions to fit your needs, ensuring compatibility with ANSI roller chains and various bore types.
Conveyor Sprocket for Sale
Applications and Performance in Argentine Industries
TEBSA’s conveyor sprockets power a wide range of industries across Argentina, from agriculture to heavy manufacturing. In the Pampas, they drive grain conveyors, ensuring efficient transport of wheat and corn to silos. In Buenos Aires, food processing plants rely on stainless steel sprockets for hygienic, corrosion-resistant performance. Mining operations in Catamarca use Type C sprockets to handle heavy ore loads, while recycling facilities in Rosario benefit from split sprockets for quick maintenance. Our sprockets are engineered for precision, with accurate tooth profiles and pitches to match conveyor chains, reducing wear and ensuring smooth operation. Materials like hardened steel and stainless steel provide wear resistance, crucial for abrasive environments like cement production. For noise-sensitive settings, such as indoor packaging lines, we offer noise-reduction tooth profiles. Online buyers searching “conveyor sprocket supplier Argentina” find TEBSA’s products reliable and cost-effective, thanks to our 50% cost edge.
Industry | Application | Sprocket Type | Benefit | SEO Keyword |
---|---|---|---|---|
Agriculture | Grain conveyors for wheat and corn | QD | Fast installation, durable for Pampas harvests | Agricultural conveyor sprocket Argentina |
Food Processing | Packaging lines in Buenos Aires plants | Stainless Steel | Hygienic, corrosion-resistant for food safety | Stainless steel sprocket for food processing |
Mining | Ore transport in Catamarca mines | High torque capacity for heavy loads | Mining conveyor sprocket Argentina | |
Recycling | Material sorting in Rosario facilities | Split Sprocket | Quick maintenance, reduced downtime | Split sprocket for recycling Argentina |
Cement Manufacturing | Belt conveyors in Córdoba plants | Hardened Steel | Wear-resistant for abrasive environments | Hardened steel conveyor sprocket |
Selection and Maintenance Tips for Conveyor Sprockets
Choosing the right conveyor sprocket ensures optimal performance and longevity. – Pitch: Match the sprocket pitch to the chain’s pin distance for proper meshing. – Number of Teeth: Fewer teeth increase speed, while more teeth boost torque. Odd-numbered teeth extend chain life by distributing wear evenly. – Material: Steel suits heavy-duty tasks; stainless steel is ideal for corrosive environments like food processing. – Bore Type: Finished bores with keyways offer easy mounting; QD or taper lock bushings provide quick setup and removal. – Tooth Profile: Induction-hardened teeth enhance wear resistance, while noise-reduction profiles suit quiet operations. For maintenance, inspect sprockets regularly for wear or debris buildup. Lubricate teeth and chains with high-quality grease to reduce friction. Check alignment using a straight edge or laser tool to prevent uneven load distribution. Replace sprockets and chains together to avoid premature wear, as worn sprockets can stretch new chains. TEBSA’s team is available 24/7 to assist with selection or troubleshooting, ensuring your conveyors stay operational.
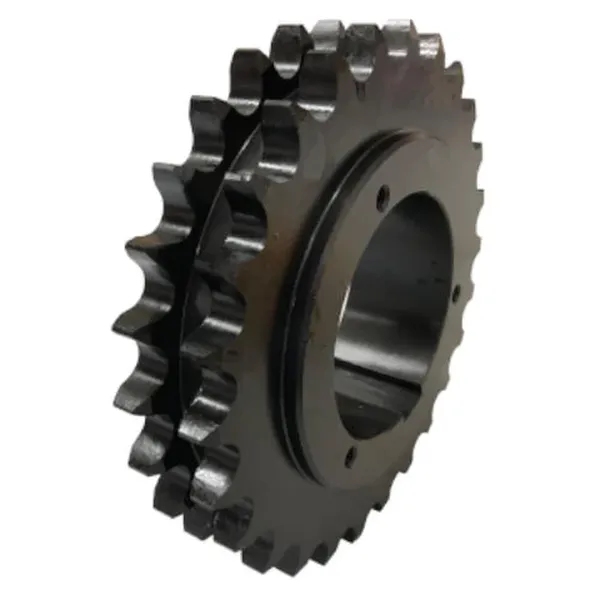
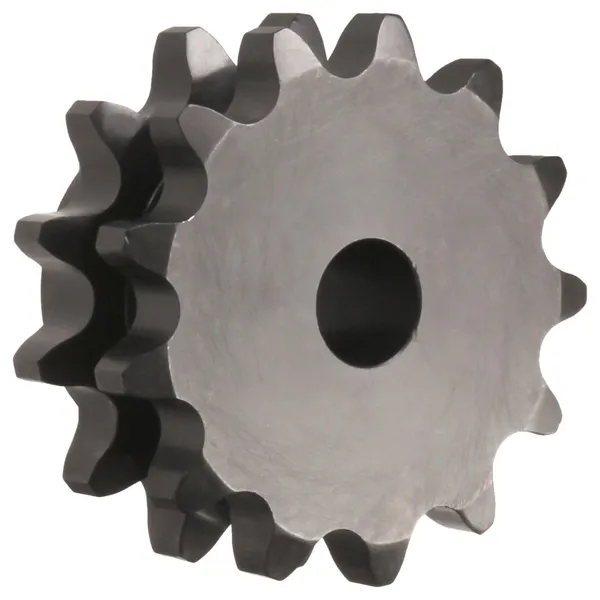
Showcase of TEBSA Conveyor Sprockets
Below are some of TEBSA’s top conveyor sprockets, designed for various applications: – FBK50B: A Type B finished bore sprocket with 50 teeth, made from C45 steel. Ideal for medium-duty conveyors in cement plants, it offers easy mounting and high wear resistance. – QD60B: A QD sprocket with 60 teeth and a quick-disconnect bushing. Perfect for agricultural grain conveyors, it ensures fast installation and uniform load distribution. – SS-A35: A stainless steel Type A sprocket with 35 teeth, suited for food processing lines. Its corrosion-resistant design meets hygiene standards.
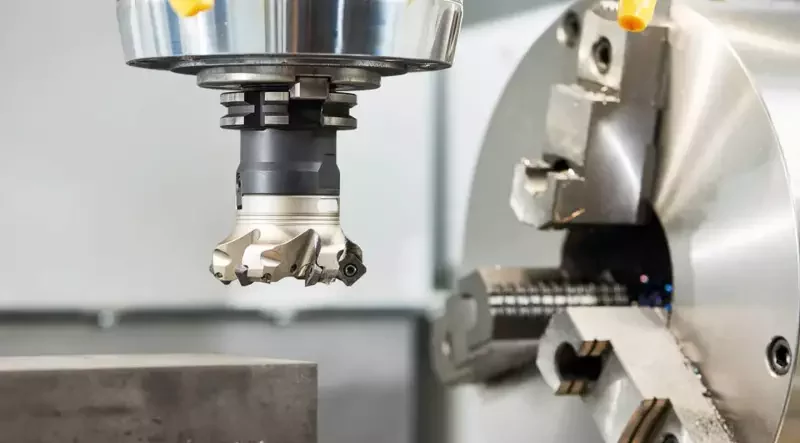
About TEBSA and Our Industrial Solutions
Since 1997, TEBSA has been Argentina’s trusted manufacturer of power transmission components, serving farms, factories, and mines with ISO9001-2015 certified products. Our conveyor sprockets, gearboxes, and PTO shafts are built using advanced techniques like forging, carburization, and induction hardening, ensuring durability and precision. With a 50% cost advantage and a 24-hour response team, we’re your partner for reliable, cost-effective solutions. Our product range includes: – Gearboxes: Like the RC-61 rotary cutter and L-25A fertilizer spreader gearboxes for agricultural tasks. – PTO Shafts: For efficient power transfer in tractors and implements. – Roller Chains: Durable chains for conveyors and machinery. – Other Sprockets: Standard bore, taper lock, and idler sprockets for diverse applications. Contact TEBSA today to find the perfect conveyor sprocket for your needs, from Mendoza to the Pampas.

Conveyor Sprockets and Conveyor Chain
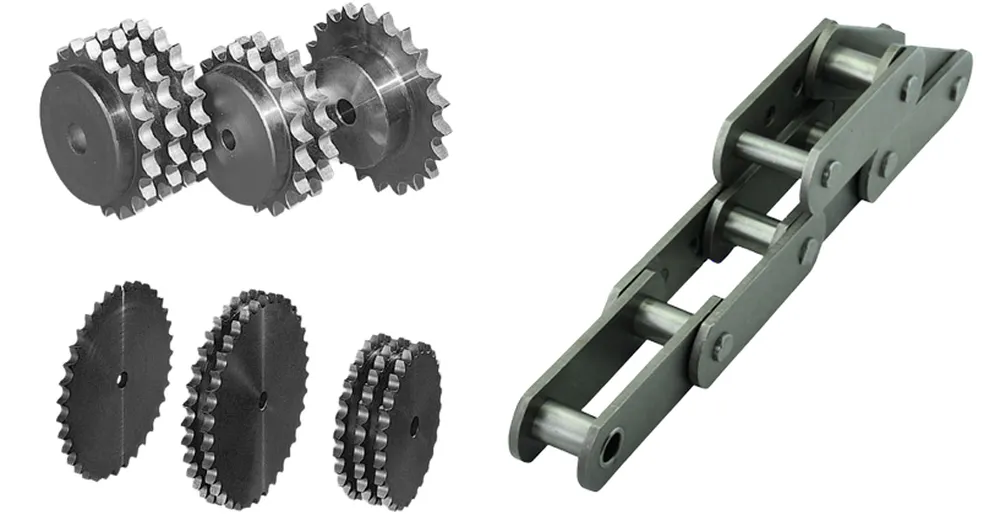
Conveyor sprockets and conveyor chains are essential components that operate together to ensure smooth and efficient material handling across diverse industrial applications. The sprocket, a toothed wheel designed to mesh with the links of the conveyor chain, drives the chain’s motion, allowing for controlled, precise transport of materials along a predetermined path. This coordination between sprocket and chain is crucial for maintaining system stability and effective load transfer.
Choosing the correct sprocket and chain combination is essential to achieve optimal performance, durability, and load distribution within the conveyor system. Available in single, double, and triple configurations, conveyor sprockets are manufactured to meet various operational needs. The choice of materials, often durable metals like high-strength steel or corrosion-resistant alloys, is determined by load requirements and environmental factors such as temperature and humidity. For high-load industrial applications, sturdy steel sprockets combined with high-tensile chains ensure extended wear life and minimal maintenance needs. Additionally, ensuring proper alignment and regular maintenance significantly reduces wear and tear, minimizing downtime and enhancing system longevity. With the right conveyor sprocket and chain combination, industries benefit from improved efficiency and reliable material handling.