Planetary Gearbox
Unlock superior power transmission with TEBSA’s planetary gearboxes, crafted for diverse uses like wheel drives, winch drives, track drives, and slewing drives across Argentina. Precision-engineered and built for durability, these gearboxes deliver strong torque multiplication, minimal backlash, and enhanced load capacity. From powering machinery in Córdoba’s factories to supporting agricultural equipment in Santa Fe’s fields, TEBSA ensures reliable performance tailored to Argentina’s needs. Trust our 25-year expertise for solutions that stand the test of time.
Planetary Gearbox for Sale
other gearboxes
TEBSA: Argentina’s Planetary Gearbox Experts
TEBSA, proudly part of HZPT, stands as a leading manufacturer of planetary gearboxes in Argentina. With over 25 years of expertise, we craft high-performance gearboxes that power industries from Santa Fe’s farms to Córdoba’s factories. Our dedication shines through in every detail—top-notch quality, exceptional service, and prices that save you 50% compared to competitors.

We prioritize your satisfaction with rigorous quality checks and ISO9001-2015 standards. Beyond planetary gearboxes, TEBSA offers a broad range of solutions, including bevel and helical gearboxes, tailored to Argentina’s needs. Rely on our unmatched skills for reliable products—contact us today for a custom quote!
Planetary Gearboxes Serve Diverse
Applications in Argentina
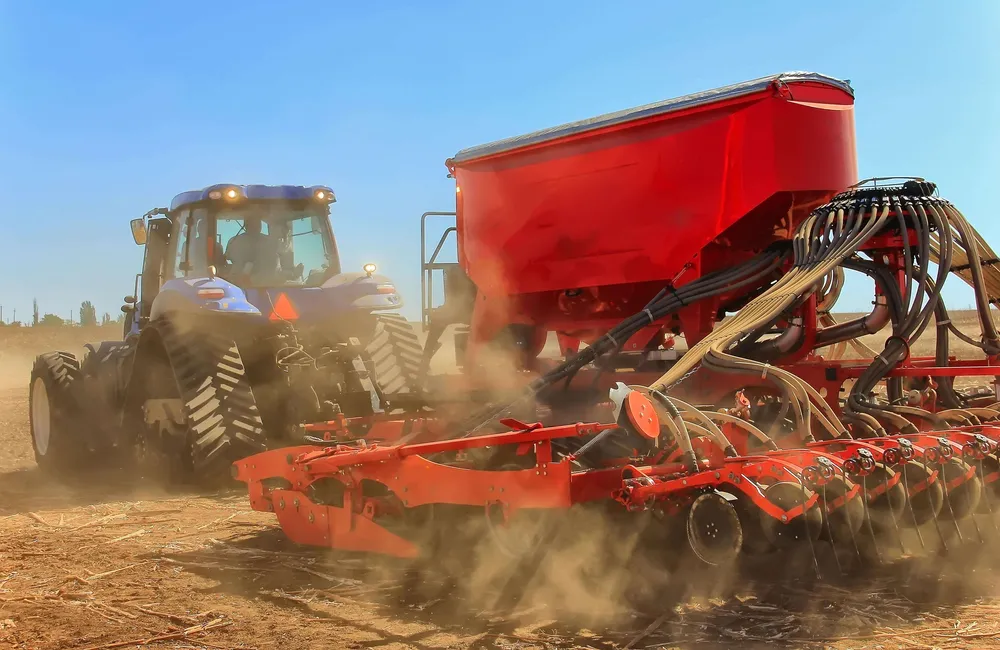
Agricultural Machinery
TEBSA’s planetary gearboxes power tractors and combine harvesters across Santa Fe’s soybean fields and the Pampas. With high-torque multiplication, they handle tough tasks like plowing and harvesting, ensuring reliable performance for Argentina’s farmers season after season.
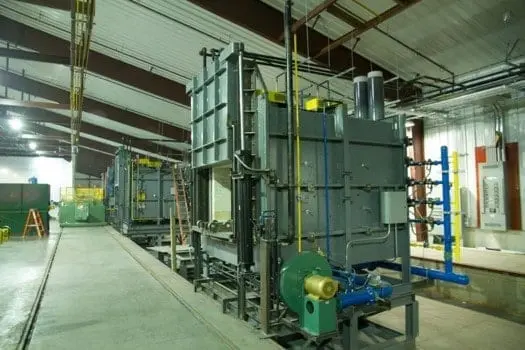
Industrial Equipment
In Córdoba’s bustling factories, our planetary gearboxes drive conveyors and mixers with increased load capacity. Their compact design fits tight spaces, delivering smooth power for manufacturing and food processing—key industries thriving in Argentina’s heartland.
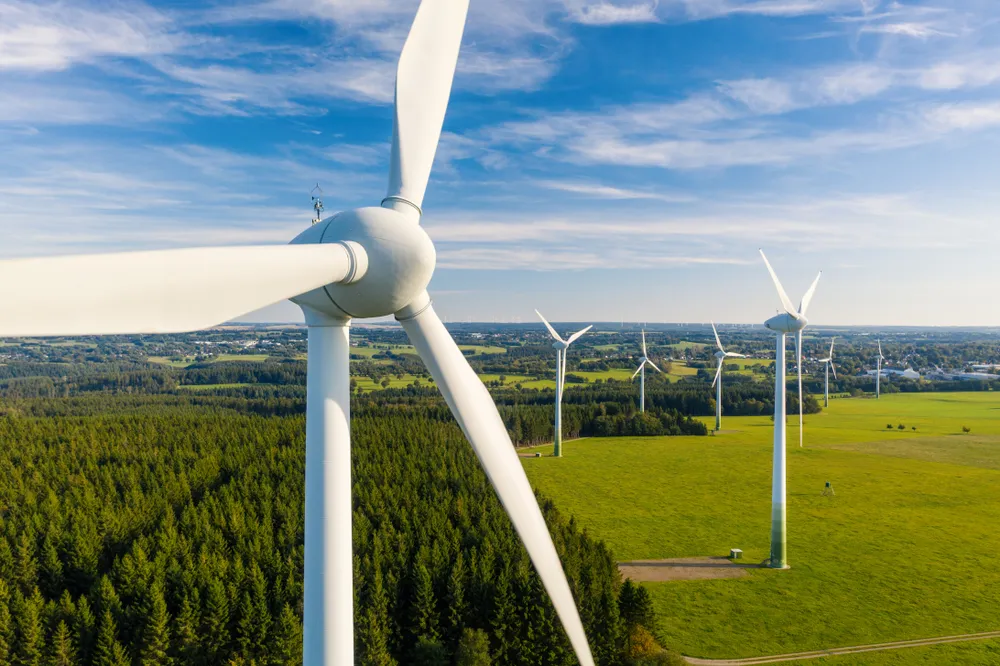
Renewable Energy Systems
TEBSA supports Patagonia’s renewable energy projects with planetary gearboxes in slewing drives for wind turbines and solar trackers. Built for durability, they endure harsh winds and long hours, contributing to Argentina’s sustainable future with efficient power transmission.
How Durable Are Planetary Gearboxes in
Argentina’s Conditions?
TEBSA’s planetary gearboxes withstand Argentina’s harsh climates, thanks to stainless steel construction and corrosion-resistant finishes. Built with precision engineering, they endure humid soybean fields in Rosario or dusty factories in Buenos Aires, lasting years with minimal maintenance—perfect for local farms and plants.
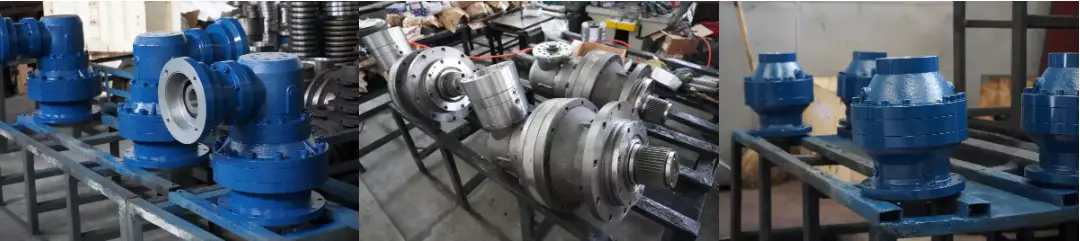
TEBSA tailors planetary gearboxes to torque needs for Patagonia cranes or applications like Mendoza wheel drives. With custom designs and 24-hour engineering support, we fit solutions to Argentina’s farms and factories effortlessly.