Plastic Sprocket
The plastic sprockets made from durable polymer materials offer superior wear resistance and noise reduction compared to similar metal alternatives. Tebsa’s nylon plastics are highly resistant to harsh chemicals and pollutants.
Plastic power transmission components do not suffer from rust like many metals, making them ideal for use in extreme environmental conditions.
Tebsa’s components are crafted from food-grade materials and feature self-lubricating properties, enhancing their durability and performance.
Plastic Sprocket Catalogue
Other Sprockets
Showing 1–4 of 25 results
Plastic Sprockets Key Features
Plastic sprockets offer numerous advantages, making them an excellent choice for a variety of industrial applications. One of the key features is their self-lubricating nature, which eliminates the need for external lubricants and reduces maintenance costs. This feature also ensures smoother operation over time, as the material itself provides the necessary lubrication for the moving parts.
Another significant benefit is their lower coefficient of friction, which results in less wear and tear compared to traditional metal sprockets. This leads to improved durability and longer service life, especially in high-speed or heavy-duty applications. Increased wear resistance further ensures that the sprockets maintain their performance, even under challenging conditions.
Plastic sprockets also provide excellent corrosion resistance, making them suitable for use in harsh environments where metals would typically degrade due to moisture, chemicals, or other corrosive substances. This resistance extends their longevity and maintains their operational integrity, even in challenging conditions.
With high impact strength, plastic sprockets are able to withstand shocks, impacts, and vibrations without compromising their performance. This makes them ideal for machinery and systems that experience sudden or variable loads. Additionally, plastic sprockets are lighter than their metal counterparts, reducing the overall weight of the equipment and making them easier to handle and install.
Another advantage of plastic sprockets is their ability to produce lower noise levels during operation. The material absorbs sound vibrations, resulting in quieter machinery, which is particularly beneficial in environments where noise reduction is a priority.
Finally, plastic sprockets can be manufactured in a variety of sizes, with split sprockets available up to 400mm in diameter, providing flexibility for different machinery and system configurations. These features make plastic sprockets a versatile and efficient option for a wide range of applications.


Advantages of using plastic sprockets
Plastic sprockets offer several advantages over their metal counterparts, especially in terms of cost, design flexibility, and performance. While metal sprockets are known for their good dimensional stability under varying temperature and humidity conditions, plastic sprockets excel in other areas, including manufacturing efficiency and cost-effectiveness. The design freedom inherent in plastic molding allows for the creation of complex shapes, such as internal gears, gear sets, and worm gears, which would be difficult or expensive to produce with metal materials.
Plastic sprockets have a broader range of applications than metal sprockets, driving the evolution of gears that can handle higher loads and transmit more power. They also play a significant role in applications requiring quiet operation, such as precision machinery, by offering excellent lubricity and flexibility. Unlike metal sprockets, plastic sprockets typically do not require secondary processing, which can reduce production costs by 50% to 90%.
Plastic Sprocket Types
The standard styles of a plastic roller chain sprocket are A-plate style meaning that there is no hub on either side of the sprocket, B-hub style which has a hub on one side; and C-hub style, which has a hub on two sides.
Standard bore styles for plastic sprockets are a stock bore, which is a plain unfinished hole in the center of the sprockets. Finished bore, which is a certain bore size that includes a key-way and two stainless steel set screws. Idler sprocket, which we can supply bearing idler plastic sprockets, bronze bore idler sprockets or plain bore style, just advise the shaft size and we supply the bore with proper clearance to idle on the shaft.
A-plate Plastic Sprocket | B-hub Plastic Sprocket | C-hub Plastic Sprocket |
![]() |
![]() |
![]() |
Durable Sprocket Solutions
At Tebsa, we offer a wide range of high-performance plastic sprockets designed to meet the diverse needs of our customers. Compared to traditional metal sprockets, our plastic sprockets provide superior durability, longer chain life, and excellent corrosion resistance. They are lightweight, reducing overall system weight, and operate more quietly, making them ideal for various industrial applications. Our sprockets are made from USDA/FDA-approved materials, ensuring their safety for use in food and drug processing. We also provide custom solutions, including snap rings, grease grooves, and specific tooth sizes, and manufacture sprockets using high-quality plastics such as nylon, UHMW, acetal, PTFE, and polypropylene. Choose Tebsa for reliable, durable, and high-quality plastic sprockets tailored to your needs.
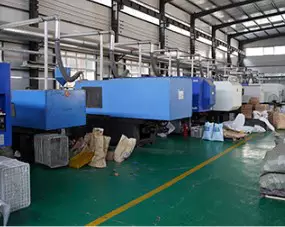
Injection molding
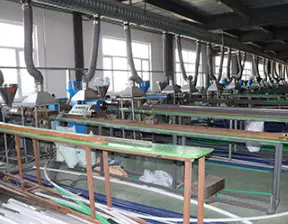
Extrusion processing
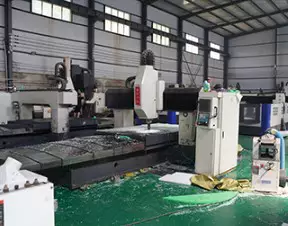
Milling machine processing
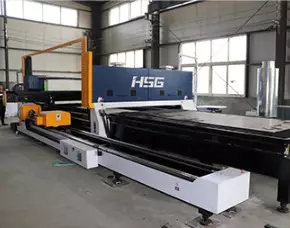
Laser zero cut
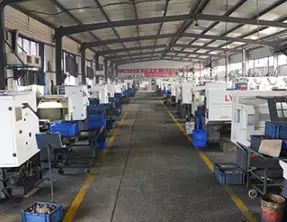
Lathe processing
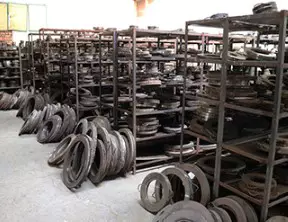