Worm gears
Discover TEBSA’s durable worm gears, built for Argentina’s toughest agricultural and industrial tasks. From flail mowers in the Pampas to conveyors in Mendoza, our high-torque, cast iron gearboxes deliver reliable performance at 50% less cost. Backed by a 100% quality guarantee and 24-hour support, TEBSA is your trusted partner for worm gear solutions. Get a quote today!
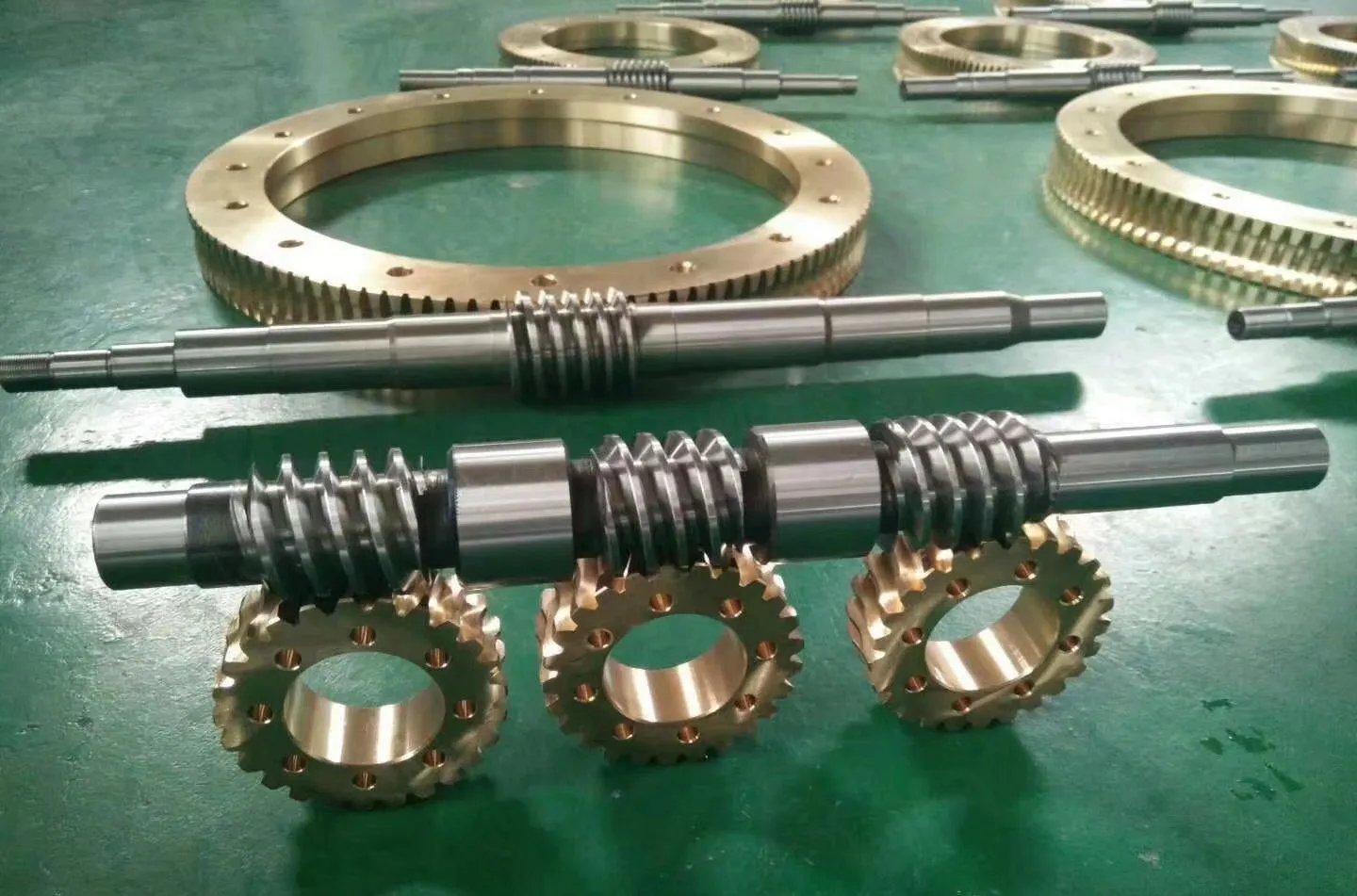
Why Choose TEBSA Worm Gears?
TEBSA’s worm gears, crafted in Argentina since 1997, are the go-to choice for farmers and industrial operators seeking reliability and value. Built with cast iron and alloy steel, our gearboxes deliver high-torque performance for flail mowers, conveyors, and more, thriving in tough conditions like the Pampas plains. With a 50% cost advantage over original brands, a 100% quality guarantee, and a 24-hour response team, TEBSA ensures your operations in Córdoba, Mendoza, or beyond run smoothly. Choose TEBSA for durable, affordable worm gears tailored to Argentina’s agricultural and industrial needs.
Worm Gear For Sale
Alloy Steel Worm
Stainless Steel Worm Gear
Brass Worm Wheel
Duplex Worms Gear
Cylindrical Worm Wheel
Plastic Worm Gears
Worm Gear Maintenance Tips
Keep your TEBSA worm gears running smoothly with simple maintenance. Fill with 80W-90 oil (check capacity for models like T-331A) before first use, and change it after 50-70 hours, then every 500-700 hours or yearly. Regularly inspect for leaks, clean and grease the input shaft, and ensure proper alignment to prevent wear. These steps, backed by our 24-hour support team, help your worm gears power through Argentina’s fields, from soybean harvests in Santa Fe to vineyard work in Mendoza, for years to come.
Applications in Argentina

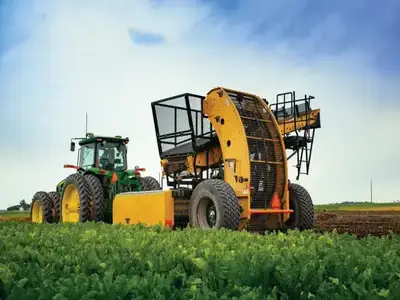
TEBSA’s worm gears power a range of applications across Argentina’s farms and industries. Perfect for flail mowers shredding soybean stubble in the Pampas, conveyors in Mendoza’s vineyards, or lifting systems in Buenos Aires factories, these high-torque gearboxes excel in demanding tasks. Their self-locking design suits precise control in agricultural machinery and industrial equipment, ensuring reliable performance for crop management, landscaping, and material handling.